Som navnet forteller, skal første byggetrinn på den 100.000 kvadratmeter store tomten stå klart 2023. Prosjektledelsen har valgt entreprisemodeller, noe som sikrer flest mulig kontrakter lokalt. Stangeland Maskin er høsten 2020 ferdig med sin leveranse av grunnarbeid og infrastruktur til en verdi av 135 millioner kroner.
For våre folk på Ullandhaug er SUS2023 et spennende prosjekt. Å jobbe med ny teknologi er framtiden, også innen bygg og anlegg. Vi har i flere år arbeidet målrettet med interne digitale løsninger og samarbeidsprosesser. Det er likevel første gang det leveres et prosjekt kun ved hjelp av 3D-modeller, såkalt bygningsinformasjonsmodellering (BIM).
BIM omfatter digital bygningsinformasjon fra A til Å i et prosjekt, hvor alle leverandører har tilgjengelig gode, digitale modeller. Det gir maks kvalitet og færre feil, og rasjonaliserer dessuten arbeidet. I stedet for å ha alt av opplysninger og informasjon i tradisjonell papirform, kan de som jobber her nå selv hente ut detaljer og all nødvendig informasjon via web. Ved å se på og eksempelvis zoome inn på konkrete detaljer i tegningene, finner man detaljer på absolutt alt man trenger å vite, eksempelvis lengder, toleranser, materialkvaliteter og høyder.
3D-modellene er enkle å forstå, og gir et reelt bilde av hvordan sykehuset vil se ut, og hvordan arbeidsprosessene er tiltenkt. Det visuelle inntrykket åpner opp for brukerinvolvering man normalt sett ikke klarer via tradisjonelle 2D-tegninger. Det gjør at løsninger kan forbedres, og at man har godt grunnlag for løpende beslutninger underveis i prosessen.
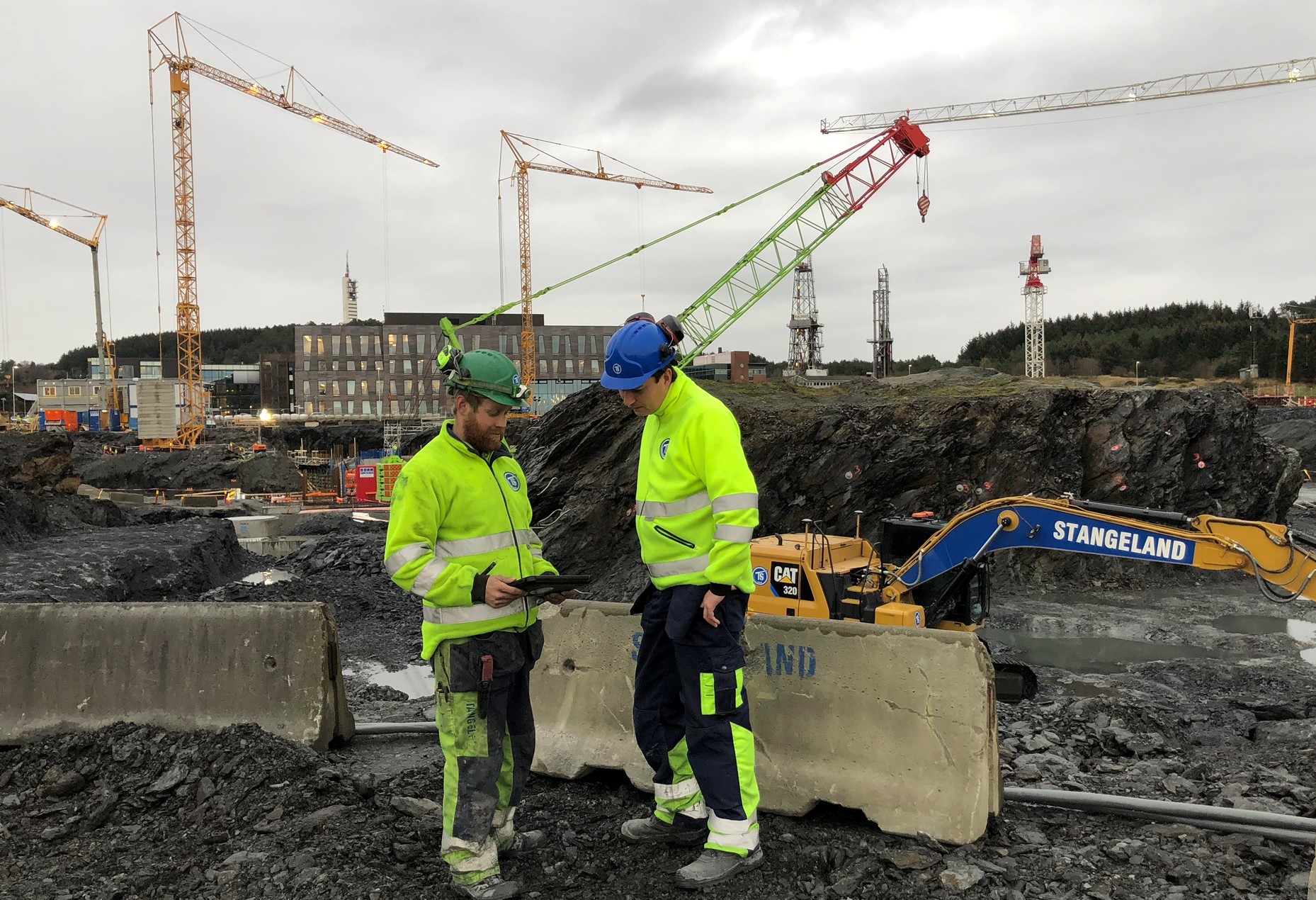
Alltid oppdatert informasjon
3D-modellene er også det Stangeland Maskin bruker som grunnlag for å planlegge og gjennomføre vårt arbeid. Stikningsingeniør Rune Osen har vært involvert i prosjektet siden oppstart våren 2019, og sammen med stikningskollegene en viktig bidragsyter for å hjelpe resten av Stangeland-gjengen til å konvertere informasjon fra 3D-modellene over i praktisk prosjektgjennomføring.
-Det er både pedagogisk og nyttig å forholde seg til 3D-modellene. Det gir oss oppdatert informasjon til enhver tid, og øker felles forståelse for hva som skal leveres, forklarer Osen. Personlig syns han det er spennende og lærerikt arbeide på denne måten, og sier han har lært mye undervegs, eksempelvis å forholde seg til fortløpende endringer og hvordan man internt på en effektiv måte justerer fremdriften basert på endringene.
Som stikningsingeniør har Osen solid kompetanse innen maskinstyring og datafangst, og jobber tett på produksjonen ute på anlegget. Det er likevel første gang han er med og drifter et rent BIM-prosjekt.
Alle som jobber på prosjektet har tilgang til 3D-modellene, enten på Ipad eller man kan besøke en av flere BIM-kiosker som er satt opp på byggetomta. I kioskene henger store skjermer hvor man navigerer seg gjennom tegningene.
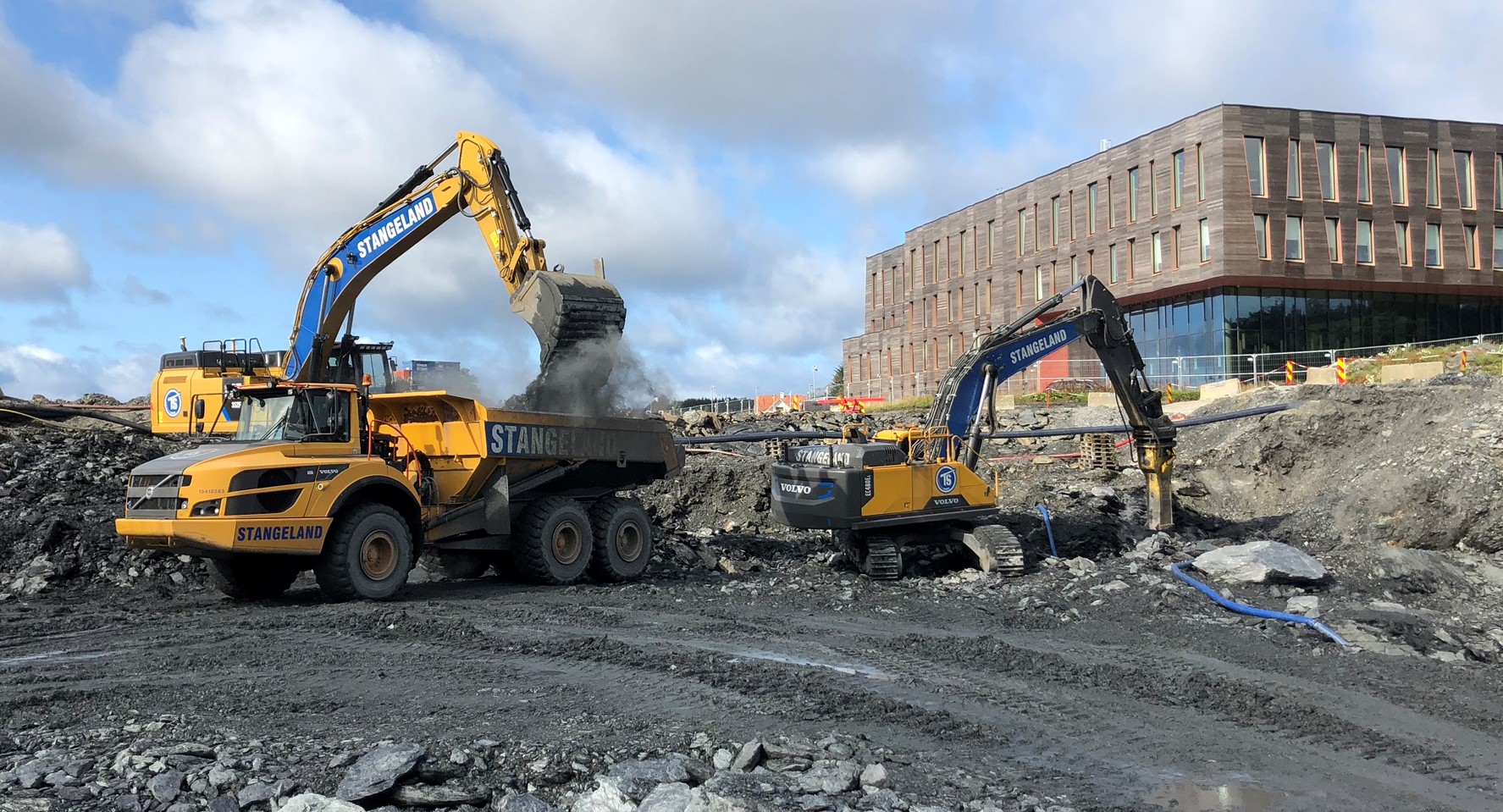
50 TS-ansatte på det meste
Ole Andraes Sørensen er grunnarbeider, og har satt seg grundig inn i 3D-modellene. Han arbeider tett sammen med stikningsingeniørene, og kvalitetssikrer blant annet høyder og fallvinkler.
-Modellene er enkle å forstå, og vi har alt av informasjon tilgjengelig. Vi vet helt sikkert at vi er på riktig lokasjon når vi drøfter løsninger for fremdrift, forteller Sørensen entusiastisk.
Rune Osen er enig, og viser rørsystem og kummer på modellen med alt man behøver å vite av detaljer. Han forklarer at informasjonen de får fra modellene, danner grunnlaget for bestillinger til underleverandører som for eksempel bend, rør og kummer.
Kjell Ove Helleland er driftsleder i Stangeland Maskin, og er ansvarlig for alt som foregår ute på byggeplassen. På det travleste har han hatt 50 TS-ansatte på anlegget samtidig. I en periode gikk 27 lastebiler i shuttletrafikk ut av tomta med masse til depot.
Totalt er det flyttet ca 460.000 m3 med løsmasse fra anlegget, det utgjør 23.000 lastebillass.
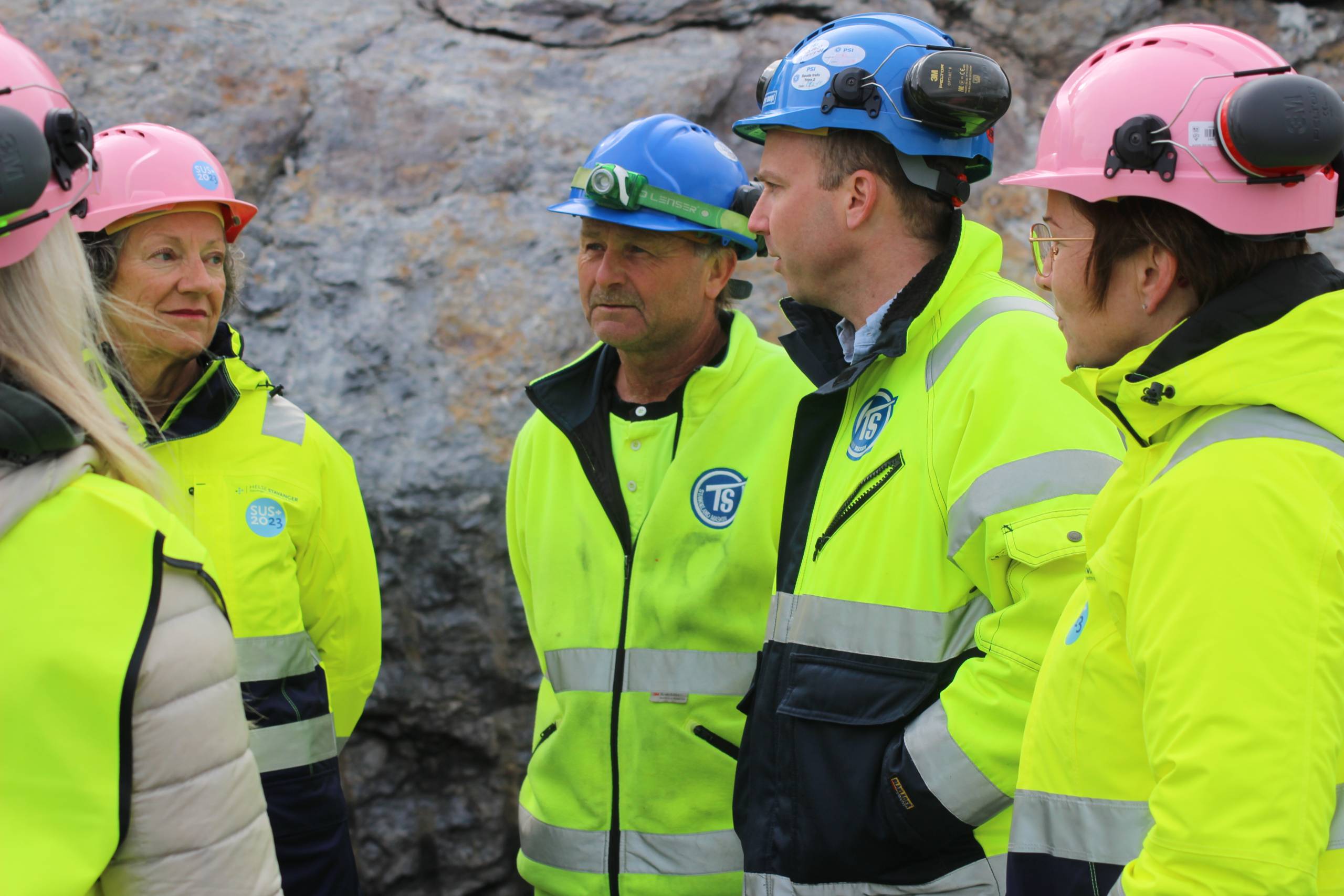
Monterer kulverter i rekordfart
-På det meste var det 9 borerigger på anlegget, og det er sprengt 300 ganger. Nå til jul er vi ferdige med bore- og sprengningsarbeidet, forteller Helleland. Den rutinerte driftslederen liker komplekse prosjekter, og mener at digitale prosjekter vil man se mye av i fremtiden.
Ikke nok med at SUS2023 er helt digitalt, her er mange store dimensjoner. For eksempel den 295 meter lange kulverten som går gjennom byggene. Hvert element har en egenvekt på hele 19 tonn, hvorav to tonn armering. Med innvendige mål på 2,5×3 meter og en veggtykkelse på 30 meter er det de største bokskulvertene produsert i Norge, og det lokalt på Sviland hos Østraadt Rør. Stangeland Maskin har designet og produsert et verktøy som brukes til monteringen. Utgangspunktet var at man i en tidlig fase regnet med å kunne montere to-tre kulverter per dag. Den nye måten å gjøre det på betyr at man på en god dag klarer å minst tredoble antallet hvor det alt i alt er 140 bokskulverter.
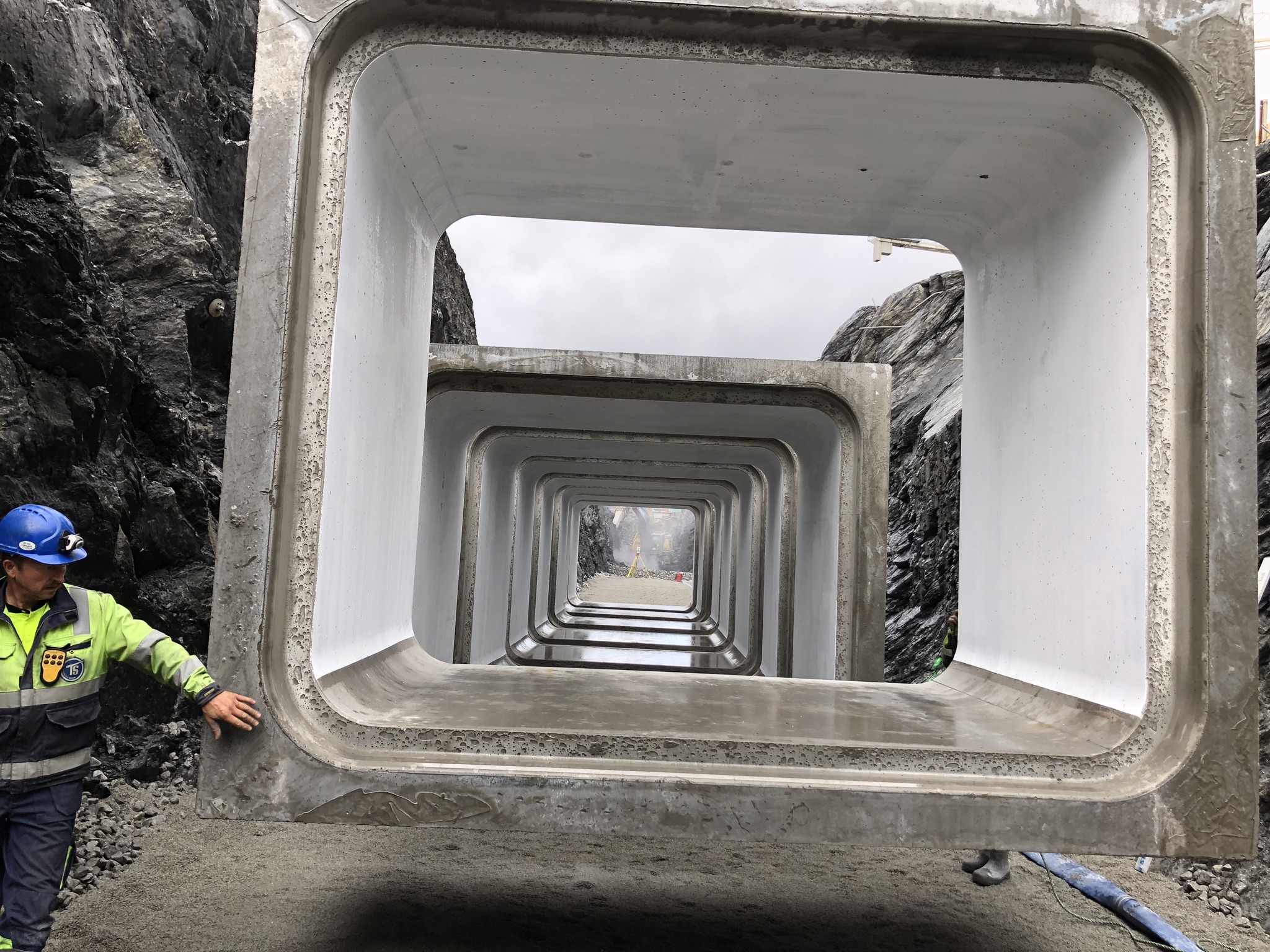